STORY #3
Creation of Ultra-High
by Nano-Meso Harmonic Structure Control
Strength and High-Ductility Materials Kei Ameyama
Professor, College of Science and Engineering
It is common knowledge, found even in basic textbooks, that materials cannot be both tough and hard. Diamond, which is solid crystal carbon, is known as the hardest material in nature; however, it is vulnerable to shock and can be easily broken if hit with a hammer at a certain angle. Meanwhile, nature provides us with some materials that compatibly have high hardness and toughness. For example, seashells, bones, and honeycombs are relatively strong and hard. How is this possible?
“Heterogeneity holds the key to this seemingly inconsistent coexistence of hardness and toughness,” explains Kei Ameyama from the Department of Mechanical Engineering, College of Science and Engineering, Ritsumeikan University, where he is currently studying heterogeneous metallic materials produced by a method called powder metallurgy.
According to Ameyama, although Japan has had prowess in traditional high technologies such as the manufacturing of the Japanese sword (Katana) since the 10th century, the development of modern Japanese materials dates only to the early 20th century, when metallurgist and inventor Dr. Kotaro Honda invented a magnetic-resistant KS steel. Initially, engineers struggled to develop high-strength materials such as hard steel; around 1980, interest in “ultra-fine-grained materials” increased to become one of the central players in material development.
Materials are accumulations of crystals. It is well known that the smaller each crystal, the harder the material. Japanese material development has pursued the creation of very small crystals as its ultimate goal. However, as mentioned, homogeneous materials cannot be hard and tough simultaneously. An increase in hardness leads to a decrease in ductility and toughness. However, this is not the case for heterogeneous materials.
Ameyama and his laboratory team purchased packs of metal powder with diameters of several tens of micrometers (half the width of a human hair). They put the powder in a mixing device with small milling balls and argon gas, and rotated this device at high speed to deform the surface of the powder to have nanocrystals on the surface.
“We refine the powder surface halfway to keep the core of the powder unaffected,” Ameyama explains. “The internal structure of the processed powder looks just like that of a boiled egg; the core is surrounded by a layer of nanocrystals, as the yolk is surrounded by the white. We call this boiled-egg-like structure a ‘nano-meso harmonic structure’.” The team then processed the powder into 3D materials using a method called powder metallurgy. First, they collected powders with harmonic structures. Then, they sintered the powder at elevated temperatures with a mold in vacuum. With this process, they could fabricate materials with both high hardness and toughness, in any desirable 3D shape.
The idea of powder metallurgy is actually not new; it is widely used in present-day industries from oil-impregnated bearings and automobiles to smaller products such as watch casings. It is expected to be more sustainable than casting, as it can reduce metal waste, which causes yield loss and cost increase.
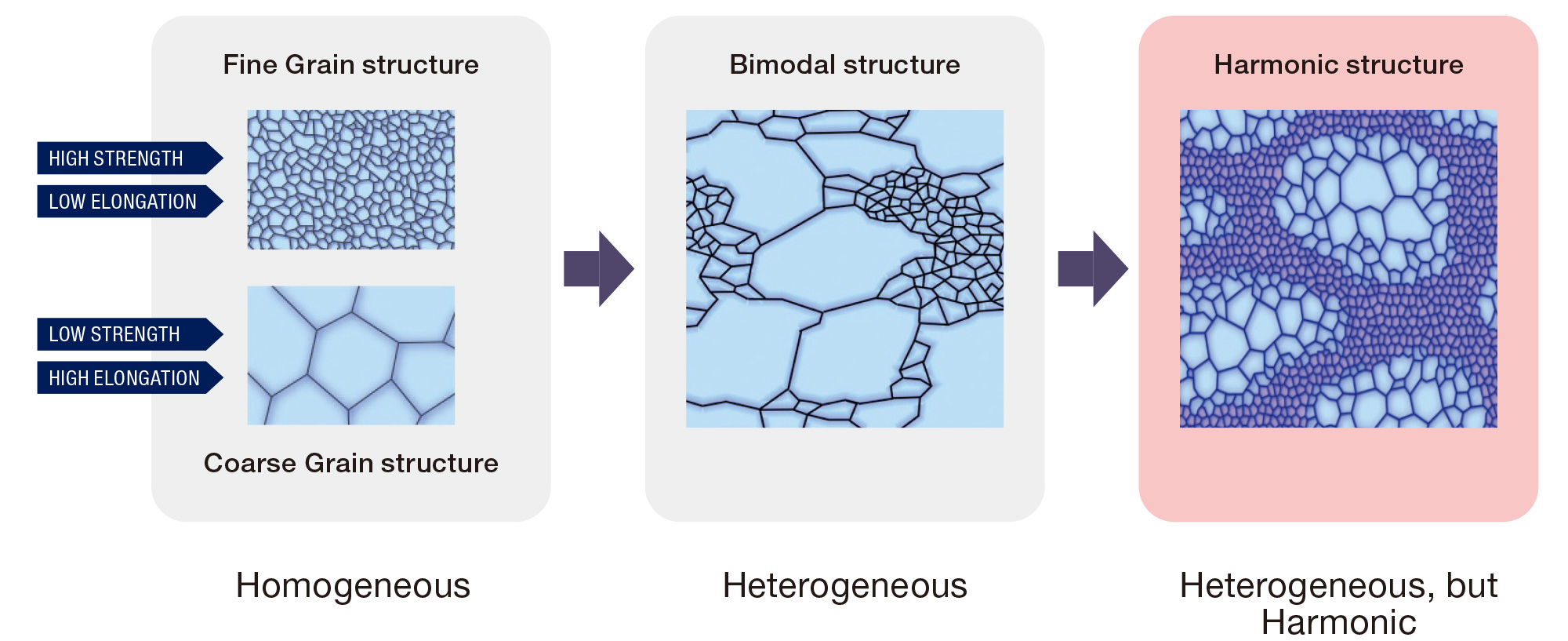
Ameyama defines his specialty as basic science, even though he is part of the Department of Mechanical Engineering, which focuses on applied science. Ameyama recalls, “I entered university just before the oil crisis in 1974. Two years prior, senator Kakuei Tanaka, who later became the Prime Minister of Japan, proposed ‘Nihon Retto Kaizoron (Building New Japan)’, and most Japanese started to realize that we should address our material and energy shortage. Civil, petroleum, and atomic engineering majors became explosively popular, and, like many other classmates, I chose my major in materials science.”
Ameyama emphasizes that he finds metallic materials intriguing because they alter their nature and appearance depending on various conditions, including temperature and pressure. He admits that the number of researchers studying metals is currently declining; more researchers have been shifting their specialty to advanced materials such as functional materials, biomaterials, electronic materials, and so on. However, he is confident and proud of his current specialty. Ameyama enjoys observing the variety of metal behavior. He prefers a tangible research target, rather than searching for methods to observe objects that are small or far away.
“In 2005 or 2006, I happened to fail at producing a homogenous nanocrystal powder in the mixing device,” Ameyama remembers, “I was processing uniform nanocrystals, and mistakenly stopped stirring too early, only to obtain a heterogeneous, halfway-crystalized powder which at that moment I regarded as useless. However, I did not want to waste the product, and decided to examine its nature. The result was unexpectedly wonderful — the powder had a nano-meso harmonic structure!” This incident motivated Ameyama to pursue powder metallurgy with a heterogeneous powder possessing a harmonic structure.
Processing powder with a nano-meso harmonic structure is not always that simple. In Ameyama’s laboratory, students are currently struggling to find methods to process aluminum and copper surfaces, as they are so soft that they easily stick to each other before their surfaces are crystalized. Temperature and humidity also affect the success rate of crystallization.
“One interesting aspect of materials engineering is that not everyone can succeed despite everyone working according to the same manual,” Ameyama smiles. “If you are assembling a machine, all you have to do is to fit all components in accordance with the blueprint. However, if you are processing a material, this is not the case. You need to have some sort of craftsmanship, which, honestly, I cannot precisely describe; some students conduct experiments much better than others, even if all of them are working in the same way.” Isn’t this similar to the instincts of a chef in a restaurant?
As material development requires a broad knowledge of engineering, Ameyama admits that it is not realistic for him and his team to work on all research and experimentation by themselves. His team’s responsibility is to process materials and evaluate their basic characteristics; other teams within and outside Ritsumeikan University are responsible for the fatigue and functional tests, as well as computer simulations of the deformation behaviors. Ameyama emphasizes, “We have so many tests and experiments to do. Teamwork is indispensable in material studies.”
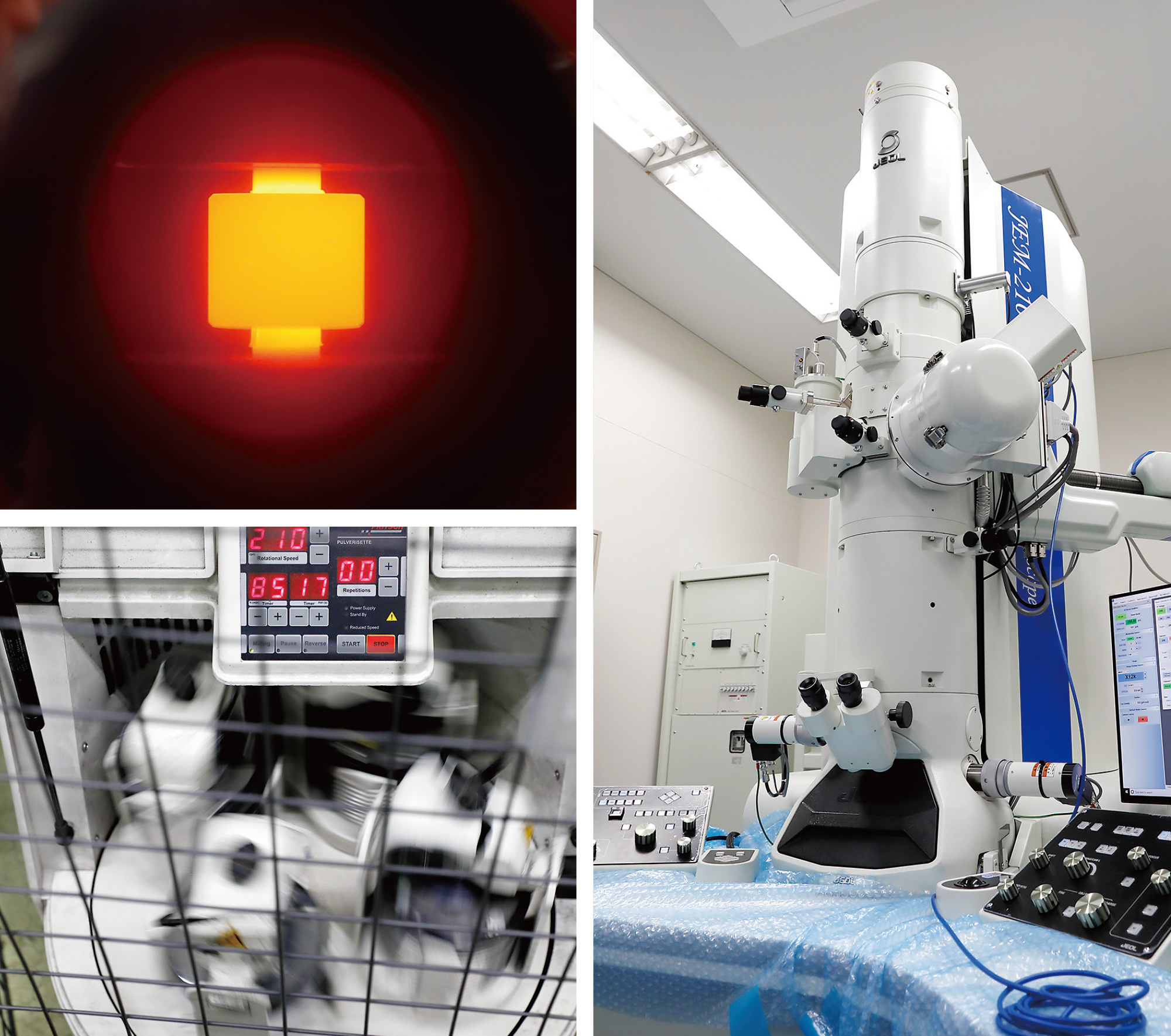
Developing the new materials by using the advanced equipments. Seeking for material's sophisticated mechanism by high-resolution electron microscope.
Heterogeneous materials can absorb collision energy, and have high torsional strength. This nature is common to all metallic materials, and Ameyama currently works with titanium, which is widely used in the present-day industry.
Ameyama explains, “Tough materials can be molded small, and are sufficiently reliable to be used in the human body; on the other hand, stronger materials can be down-sized and are sufficiently light to be applied in aerospace engineering. Currently, I am mostly working on developing small and robust medical tools, namely scissors and knives for laparoscopic surgeries, as medical devices are less expensive and have a larger demand than aerospace machinery.” He recalls that, several years ago, he was asked to investigate a medical accident in which a pair of metal scissors got chipped in the patient’s body. The group of surgeons had reported that the scissors were not sufficiently strong and tough and that one of the tips broke during the surgery. Ameyama learned how crucial it is for medical personnel to work with tougher and more robust equipment.
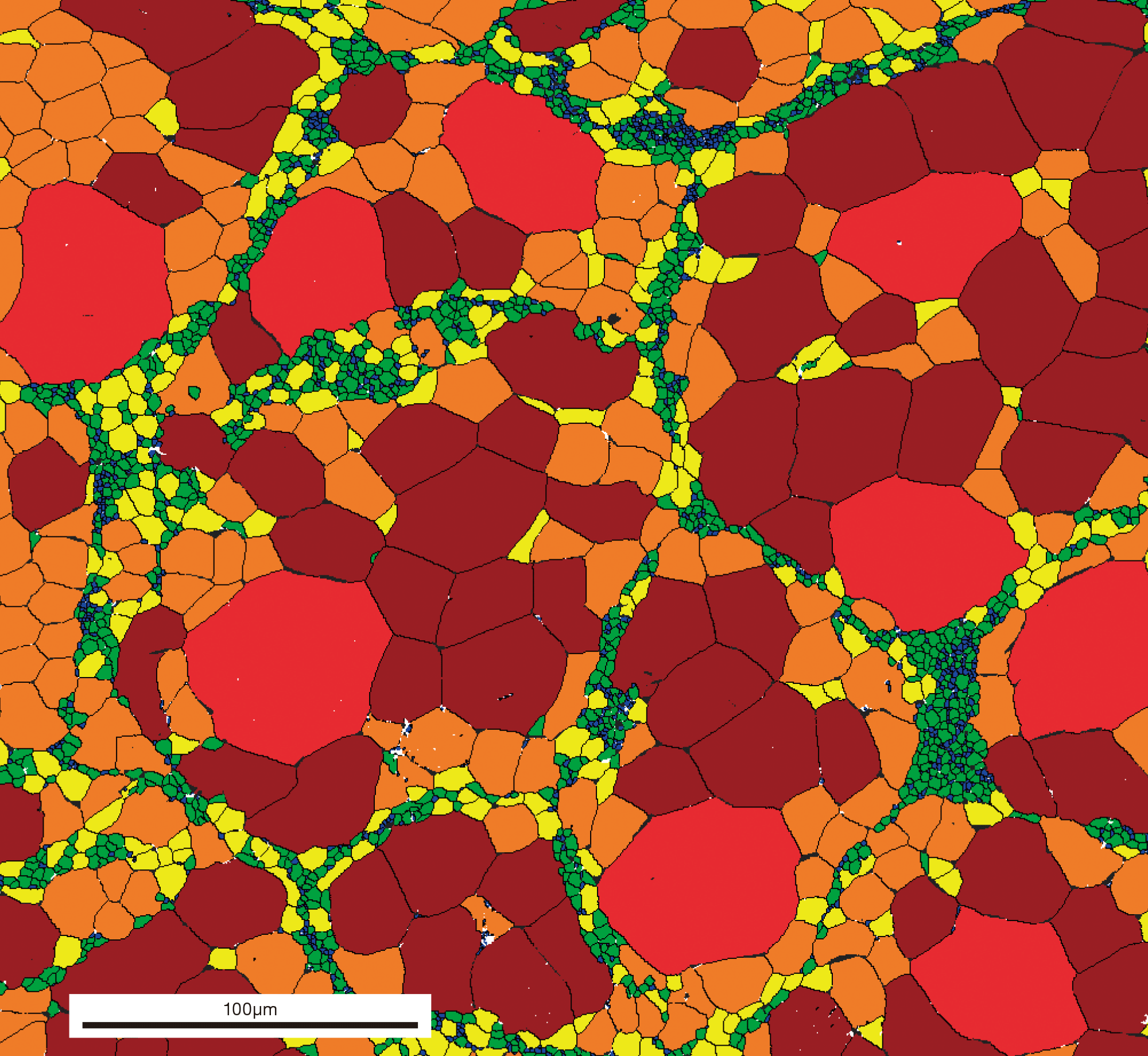
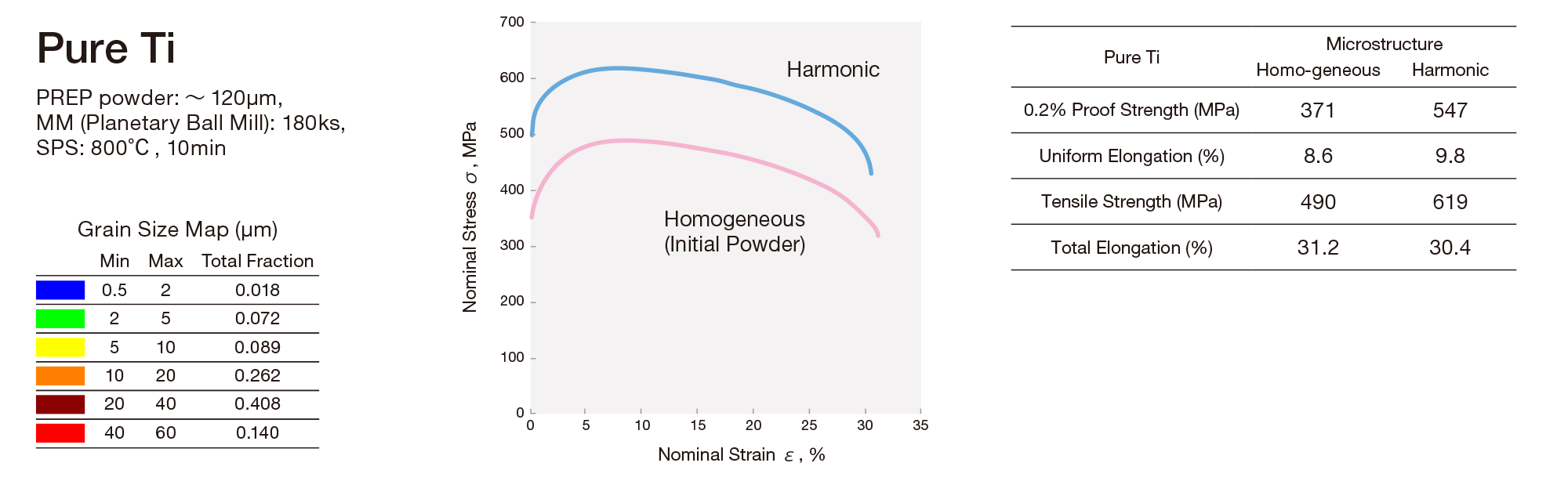
Ameyama has recently become interested in nonmetal materials as well. He emphasizes that it is the universal nature of heterogeneous materials that piques his curiosity, and points out that there are several heterogeneous, hard, and tough nonmetal materials in our immediate surroundings. “Concrete, for example, composed of coarse and fine aggregate (gravel and sand), and cement,” he illustrates.
Material development requires long, sustained research. It is not uncommon these days that researchers have to wait for 30 or 40 years before their work is finally commercialized. “Things never work out as you expect, but the excitement of materials engineering lies just inside of this unpredictability,” Ameyama advises young followers. “I had my then-research purpose and was testing my hypothesis when I ‘mistakenly’ invented powder which had a nano-meso harmonic structure. Strictly speaking, I failed in that experiment. I never expected to create something useful until I tested the material. Do not be afraid of failure. Do not waste any products obtained from your experiments; always test them. Lady Luck favors researchers who are bold and curious.”
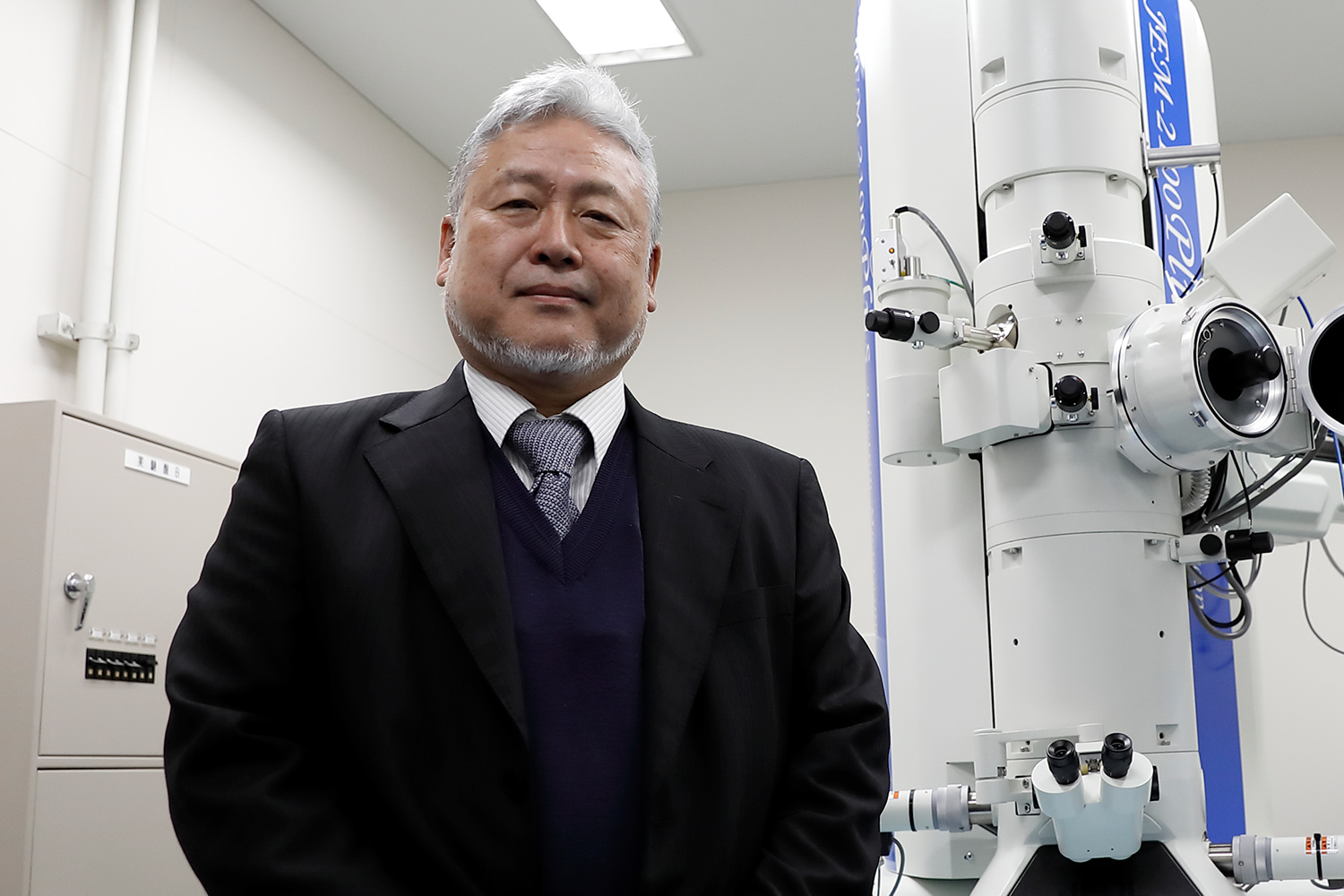
- Kei Ameyama
- Professor, College of Science and Engineering
- Subject of Research: Material control and structural analysis of metal and ceramic materials, and the development of ultra-high strength and high ductility materials Research Keywords: Materials Science and Engineering, Structual and Functional Materials, Metallurgy and Material Processing
*The interview for the article was conducted in April 2019.