STORY #2
Developing Soft Robot
End Effectors to
Grasp Multiple Items
Sadao Kawamura
Professor, College of Science and Engineering
Convenience stores provide a variety of bento meals (i.e., rice and accompanying dishes packed together in take-out packages) every day. Side dishes depend on the season or the trends, and one can enjoy hot and healthy meals from very early in the morning to very late at night. However, who is preparing these meals? Are there automated bento factories? Are there robots packing every dish? The answer is no. These meals are packaged by people with their own hands. But why do convenience store companies not automate this time-consuming task?
“Robotic handling of materials is not completely practical, especially when it comes to handling soft material like food,” reveals roboticist Sadao Kawamura, professor at the Department of Robotics, College of Science and Engineering, Ritsumeikan University. According to Kawamura, the hands of present-day robots cannot yet adjust their grasp according to various object shapes and/or for soft materials, as human hands do. This is one of the reasons behind Kawamura’s claim that “the mass media usually makes a fuss about robots and artificial intelligence replacing humans in the work place, but I believe it won’t apply to material handling, at least for the time being; in fact, they are always short-handed and have to rely on imported labor.”
The bottlenecks of technology include recognition, mechanism and control, and implementation. Regarding recognition, audio-visual sensors are way ahead of other sensing technologies. The Big Four (Google, Amazon, Facebook, and Apple—also referred to as GAFA) have dominated¸ the current IT industry with their audio-visual sensing technologies, including facial recognition and voice dictation. Cyber eyes and ears are now either equivalent to or in the process of transcending our physical ones, and information detected by them is easily shared on the Internet. However, the same ubiquity of information has not yet been applied to tactile or force sensors.
“Robots have fingers or hand-like devices connected to their arms to touch or grasp materials; the devices are called end effectors. It is a difficult task for end effectors, even with touching, weight, and force sensors, to take delicate actions such as quickly picking up a paper cup; however, most of the commercialized end effectors are neither equipped with those sensors, nor are they connected to the Internet, and we are struggling to accumulate and send physical information on our servers or the cloud,” Kawamura explains.
It might sound queer, but commercialized material-handling robots do not have the “physical touchsensing” to handle objects. As mechanism design theory and control theory have not yet fully matured, it is still challenging for developers to make robots firmly grasp or assemble soft materials and/or multiply shaped objects. “I want to break through the wall,” Kawamura says emphatically, adding “my plan is to create a soft end effector, equipped with lots of sensors. I don’t stick to the shape of the human hand; academia thinks highly of it, but it is not necessarily the most efficient when it comes to industrial application.”
Making the end effector soft is one of his key considerations. He highlights the benefits of this softness, saying “Controlled with edge computing, soft end effectors can safely grasp and handle soft materials.” Use of polymetric material and 3D printing technology are also unique features of his approach. “Polymers have rarely been used in industrial robots, but I believe they would open up the path to light, flexible, and foldable robots. If robots were made completely out of plastic, we wouldn’t have to worry about the adverse effects of the electromagnetic field on them. In recent years, 3D printing—or additive manufacturing—has made remarkable progress and can be applied to not only plastics but also metal, and gel. With this technique, prototyping and modeling is becoming much faster and easier.”

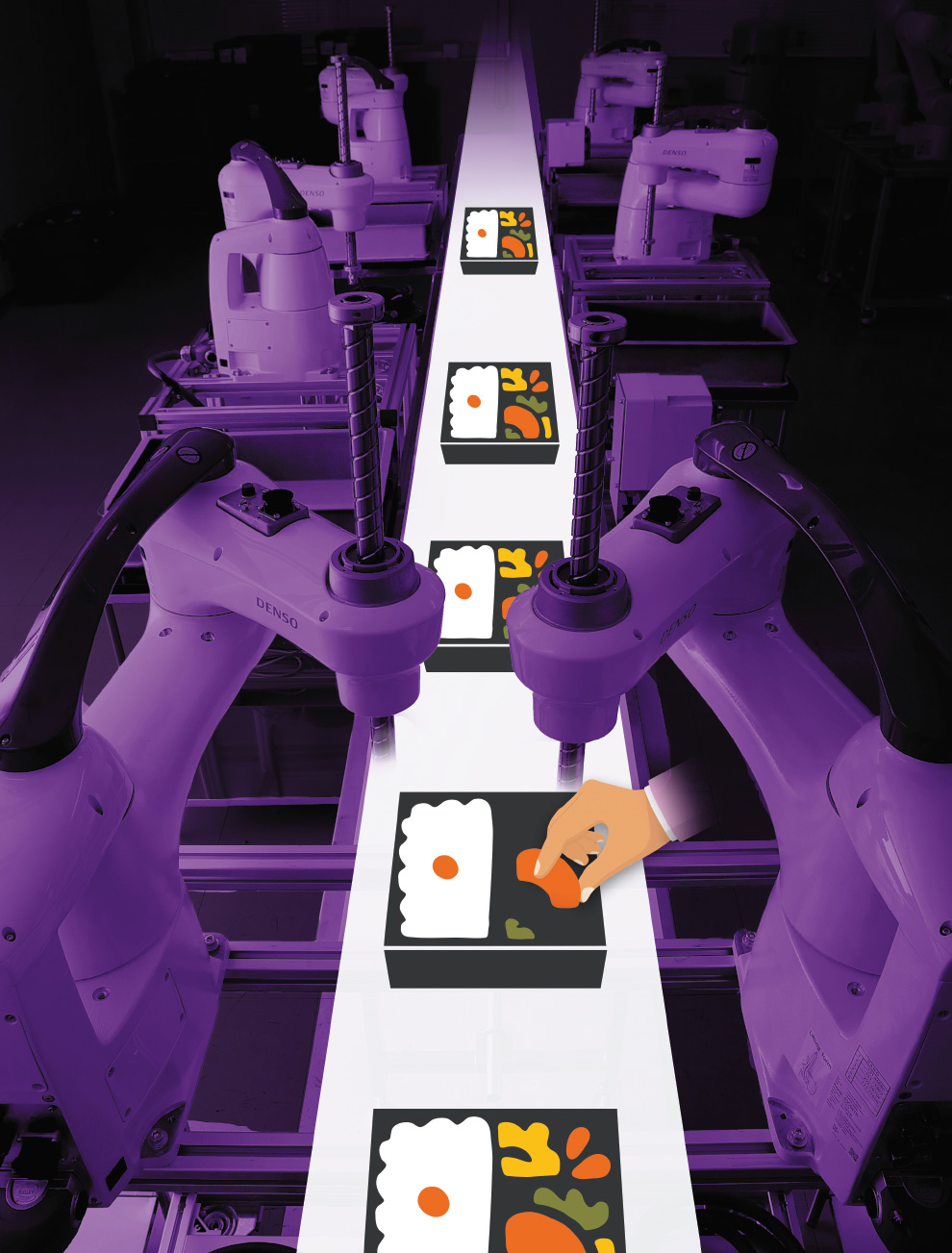
Kawamura recalls when he first gained interest in robotics, a symbol of modern science. “Like many other children, I too watched the famous TV program ‘Astro Boy’ and was thoroughly entertained by the story. However, I knew that Mighty Atom was not the robot I wanted to create.” With age he realized he was curious also about the movements of animals and started to wonder whether he could apply animals’ abilities to robots. Kawamura started studying biomechanics and later switched his major to mechanical engineering to learn more about robotics.
“I am not mimicking the human hand, even though I have learned the principle of the human hand movement,” emphasizes Kawamura. “Mimicking hands, while familiar and acceptable, is not the optimal solution, nor is it a goal in life evolution. It is true that it is effective, but we must admit that sometimes it is ineffective as well.” Kawamura mentions the so-called Cambrian explosion, an event that took place approximately 540 million years ago, which refers to the sudden and explosive appearance of complex animals in the fossil record, to illustrate the importance of diversification. “Some robots can be hard; some can resemble human hands. But they still cannot cover the different needs of different industries.” Kawamura also reminds us that robot–human cooperation might be an illusion. “Sanitation is the most important aspect of food handling,” says Kawamura, adding “and humans carry bacteria in their bodies. Getting rid of humans results in cleaner food factories. Food will last longer in the fridge than at room temperature, and there are some food items and drinks whose taste deteriorates when exposed to light. If there were no humans around, robots could work in the environment that is best suited for the particular food item.”

Kawamura is now working with around 15 laboratories inside and outside Ritsumeikan University. Kawamura’s lab is responsible for developing a control algorithm and analyzing the dynamics of finger-like end effectors actuated with air pressure. The other labs are in charge of key technologies such as new material development, etc. Kawamura manages this development project in its entirety.
“First, we had to be aware of each industry’s needs,” Kawamura explains. “We also had to learn what the 15 labs were good at, in order to combine our technologies and expertise. We have also asked many private companies to cooperate with us.” As a part of the industry–academia collaboration, one of the graduate students established Chitose Robotics Inc. in Kawamura’s lab in 2018, with Kawamura as one of its directors. Chitose Robotics Inc., a system integrator company in Japan, developed and merchandised a new, automated dishwasher system. The company is working on verifying the robotization of the dish-washing process. “We set up a mock kitchen and sink in our lab, installed some industrial robots, and started testing them. Dishwashing is a time-consuming task and physically tasking too, as the dishes are heavy and one always has to bend while washing them. We provided our new motion-control methods to demonstrate picking up, carrying, and stacking dishes.”
Kawamura emphasizes that as they are aiming to develop their findings for practical use, their robots should have a minimalistic design and be relieved of too many parts and equipment that need to be especially purchased or maintained. “I said that the end effectors would have lots of sensors, but I would equip them only if they were necessary,” says Kawamura. “We have to keep studying which sensors and equipment the industry really needs.”
Kawamura’s project (the Cabinet Office (CAO), Cross-ministerial Strategic Innovation Promotion Program (SIP)) is “[A]n intelligent knowledge processing infrastructure, integrating physical and virtual domains” started in 2018 and is expected to be completed in 2022. Its major goals are developing end effectors, clarifying their mechanism, and solving their problems. As its immediate goal, Kawamura is now planning to increase the industry–academia joint projects, following the dish-washing project, before 2020. Using these startup projects as a foothold, Kawamura and his lab will cultivate future collaborations before the completion of the project in 2022.
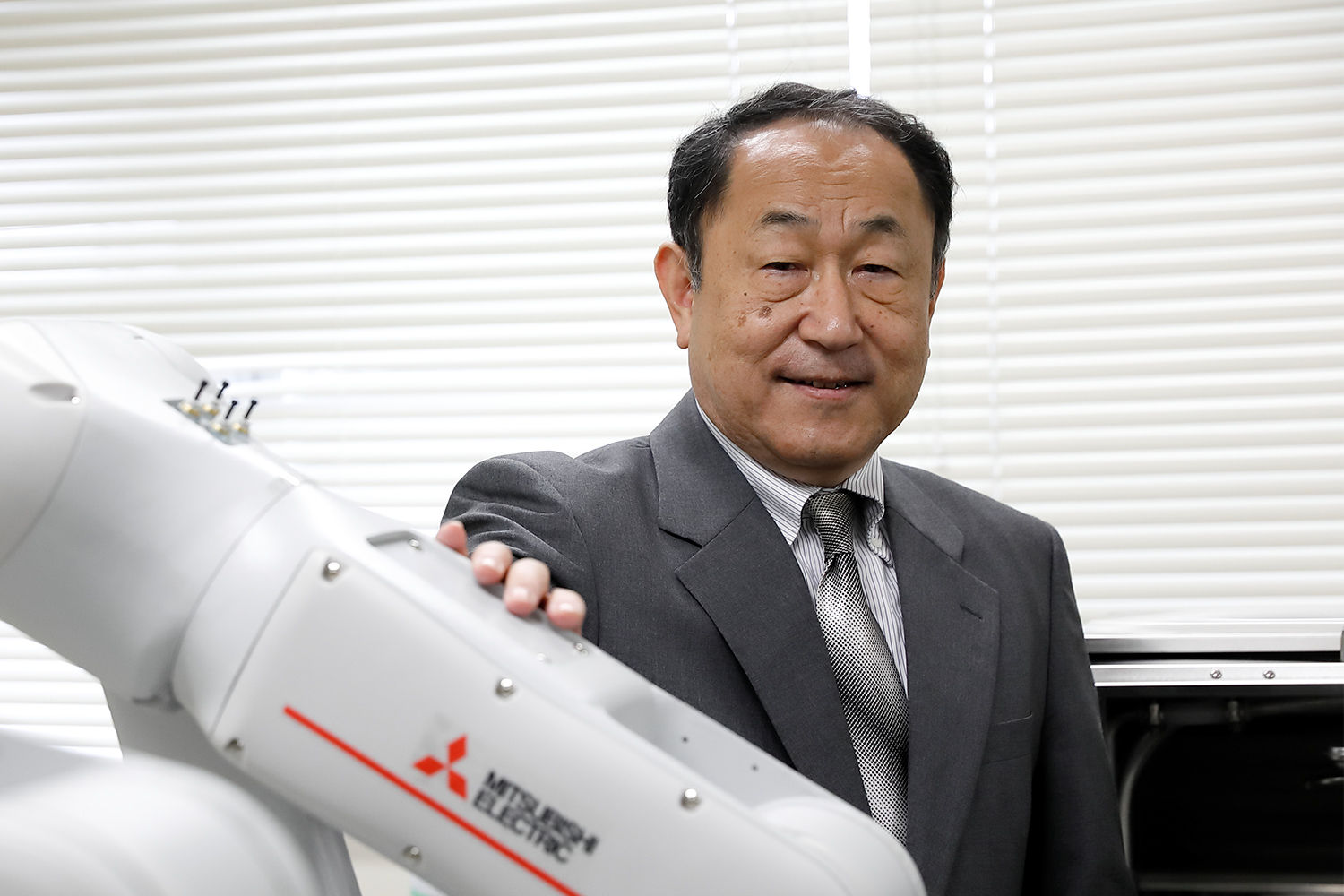
- Sadao Kawamura
- Professor, College of Science and Engineering
- Subjects of research: Robot development for underwater operations, the design and development of soft robots, and the development of next-generation industrial robots
Research keywords: Intelligent mechanics and machine systems
*The interview for the article was conducted in April 2019.