STORY #5
Robust, durable mechanical robots with a
seemingly unsophisticated appearance that are capable of fulfilling their potential at disaster sitesShugen Ma
Professor, College of Science and Engineering
Atsushi Kakogawa
Assistant Professor, College of Science and Engineering
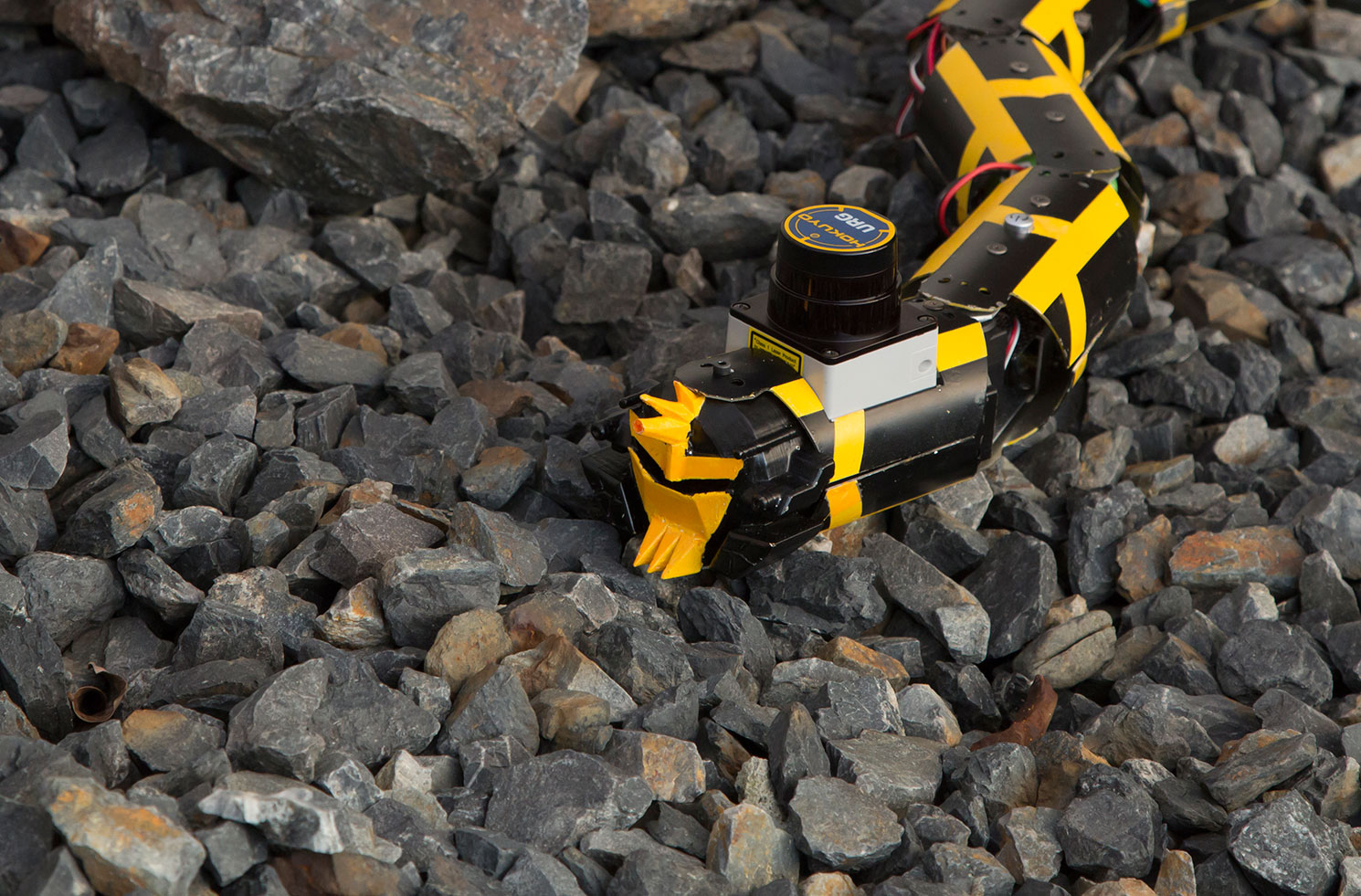
What can be done by machines should actually be executed by machines.
This is the most useful at disaster sites.
Ma said, “Our mantra is that what can be done by machines should actually be executed by machines.” According to this mantra, Ma and Kakogawa are developing robots that can be driven by only a very limited number of motors and mechanisms, with limited and simple control system rather than with complex control system. Even if software is elaborately developed, it is impossible to avoid a malfunction of the software, which occurs with a fixed probability. Such malfunctions are even more unavoidable during natural disasters and other contingencies. In this regard, their machines have the advantage of possessing higher reliability.
Kakogawa also said, “Just because the most advanced technologies can be applied for robot development, it doesn’t mean the most appropriate development of robots is achievable. Robots for disaster relief are highly expected to have capabilities for responding to contingencies or adapting to adverse environments flexibly and to be robust enough to tolerate them. The principles of physics can be applied to the design of robots too. As a reaction force is generated when robots come into contact with the surrounding environment, this force can be used as propulsion to drive the robots. Specifically speaking, robots can be designed to rotate themselves to climb over steps by using the force that is generated when their wheels contact to obstacles. Therefore, there is no need to incorporate extra sensors and actuators into the robots, and it is possible to make them more durable and consistently more reliable, smaller and lighter. Our research laboratory makes it a research policy to maximally pull out the capabilities of the mechanical systems with a less use of sensors and actuators.”
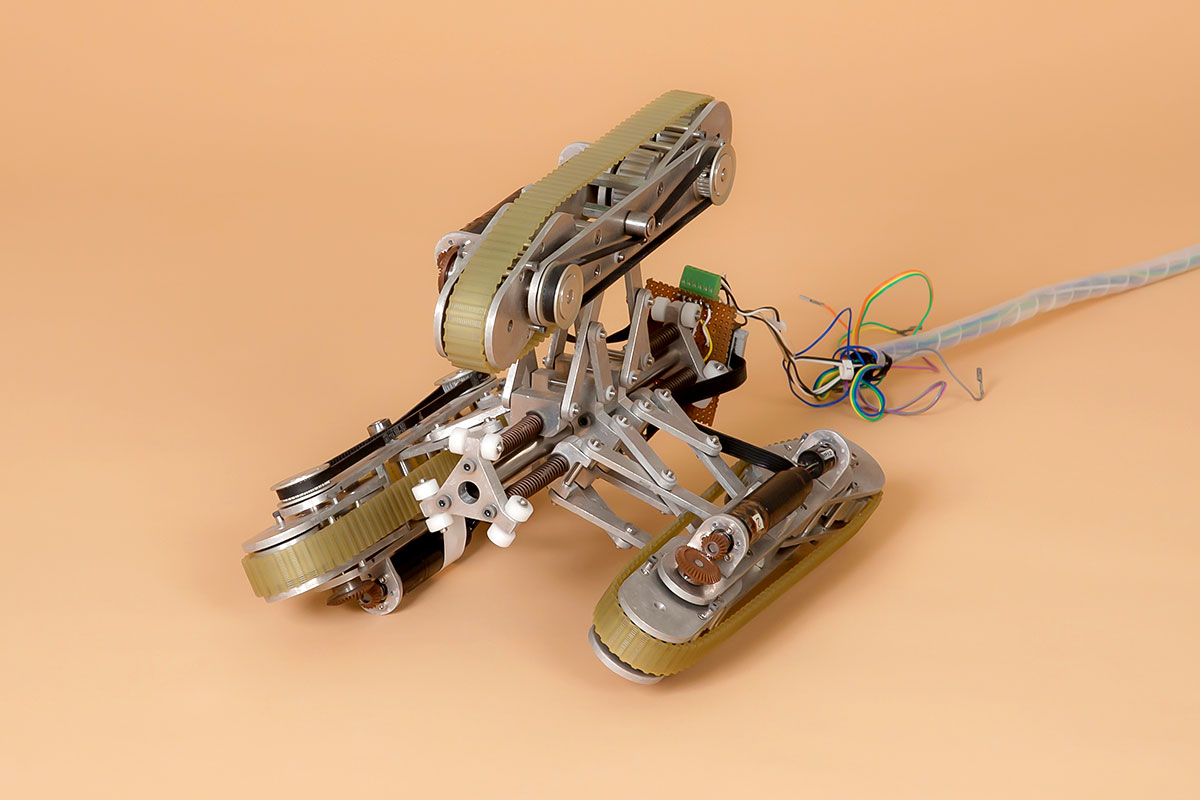
In-pipe inspection mobile robot with three modules. As the three modules are mutually connected with spring-like joints and the tip end of the caterpillars is designed to be bent, the robot can be adapted to a variety of pipes configurations for flexible movement inside a pipe.
The above mentioned features are also introduced in-pipe inspection mobile robot with three modules, developed by Ma and Kakogawa. The robot has a structure in which three independent driving modules are arranged radially. Each of these caterpillar-type modules can be independently driven because each of them is equipped with a motor. When all of these three modules are driven at the same speed, the robot moves forward. When one of them is driven at a different speed, it is possible to change the moving direction of the robot into the direction where the wheels rotating at the lowest speed are located.
As the three modules are connected with springs, the robot can be expanded and contracted flexibly even if pipes are clogged or the width of pipes narrows unexpectedly. “When designing the robot, we carefully adjusted the number of gear wheels attached to the robot. This is intended to ensure that the differential drive system will function when the robot collides with obstacles so that it can autonomously contract itself. In this way, it is not necessary to equipped with more complex driving mechanisms or sensors designed to change its shape.”
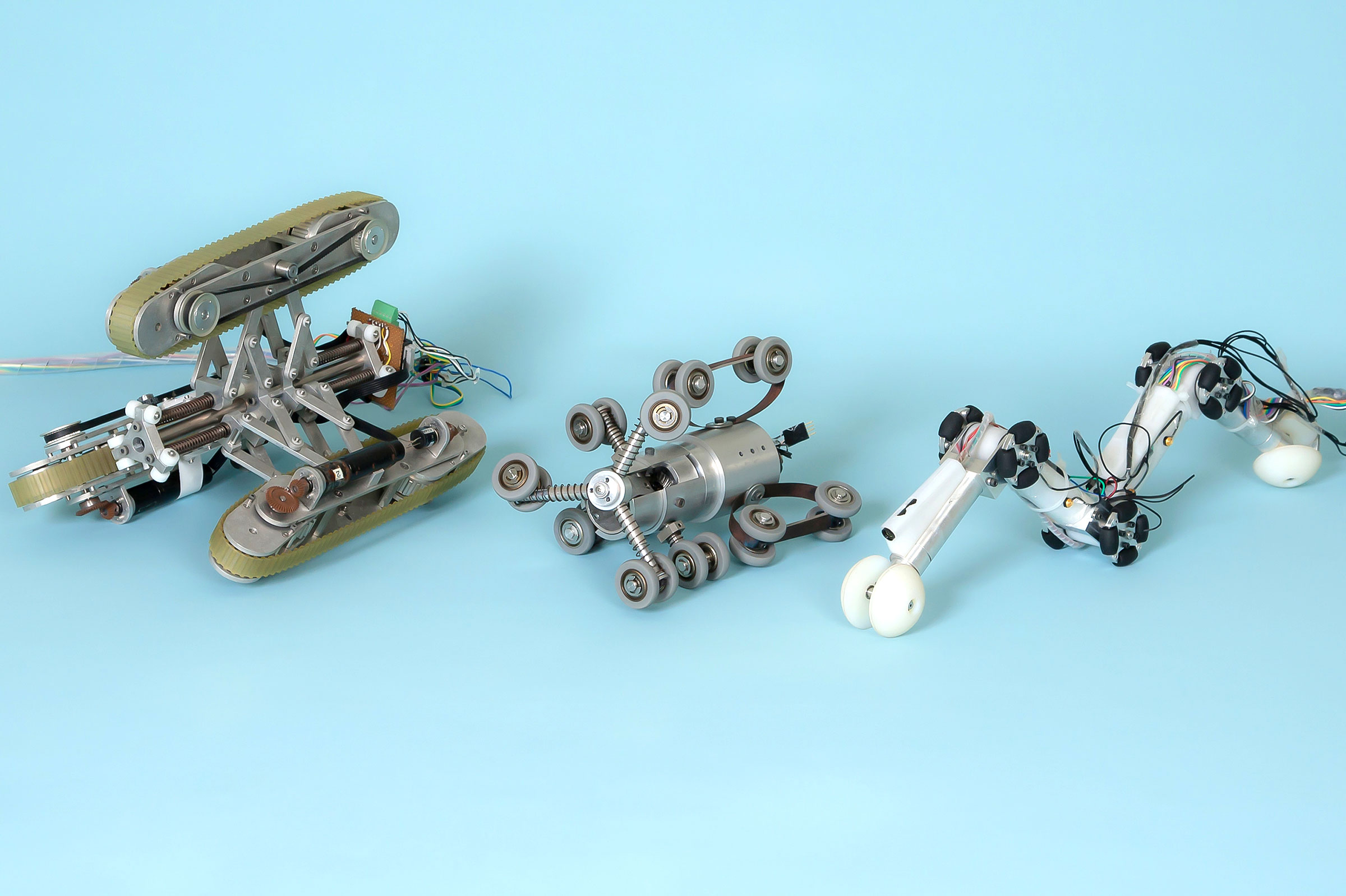
Ma said, “Our unending mission is to make robots smaller for reduced power consumption by reducing the number of motors and other actuators incorporated into these robots as much as possible.” This is because the achievement of their mission greatly affects the usefulness of robots at disaster sites.
This humorous looking robot, capable of climbing up a vertical glass wall, has caterpillars to which suction cups are installed. The robot is designed to climb on a glass wall by attaching the suction cups to the glass surface. The robot is not equipped with suction pumps to generate power supporting the weight of the main body. Taking a cue from inspired from the functionality of push-type suction hooks commonly used in households, Ma applied a mechanism in which suction cups are stuck attached to and then smoothly detached from the glass surface by the caterpillars. A great number of know-hows are applied to the robot, although its appearance seems to be unsophisticated.
This screw-driving in-pipe inspection mobile robot has wheels that always make forward movement, as well as wheels that support the main body in the three axis directions. With the three wheels attached to the front unit of the main body being inclined, the wheels can be rotated, just like screw propellers. This makes the robot move forward while the wheels move in a spiral path. Since the robot can be driven with much less force in accordance with the same mechanism as the screw drive mechanism (it is possible to move up an object in a gentler slope with much less force), the robot is suitable for miniaturization.
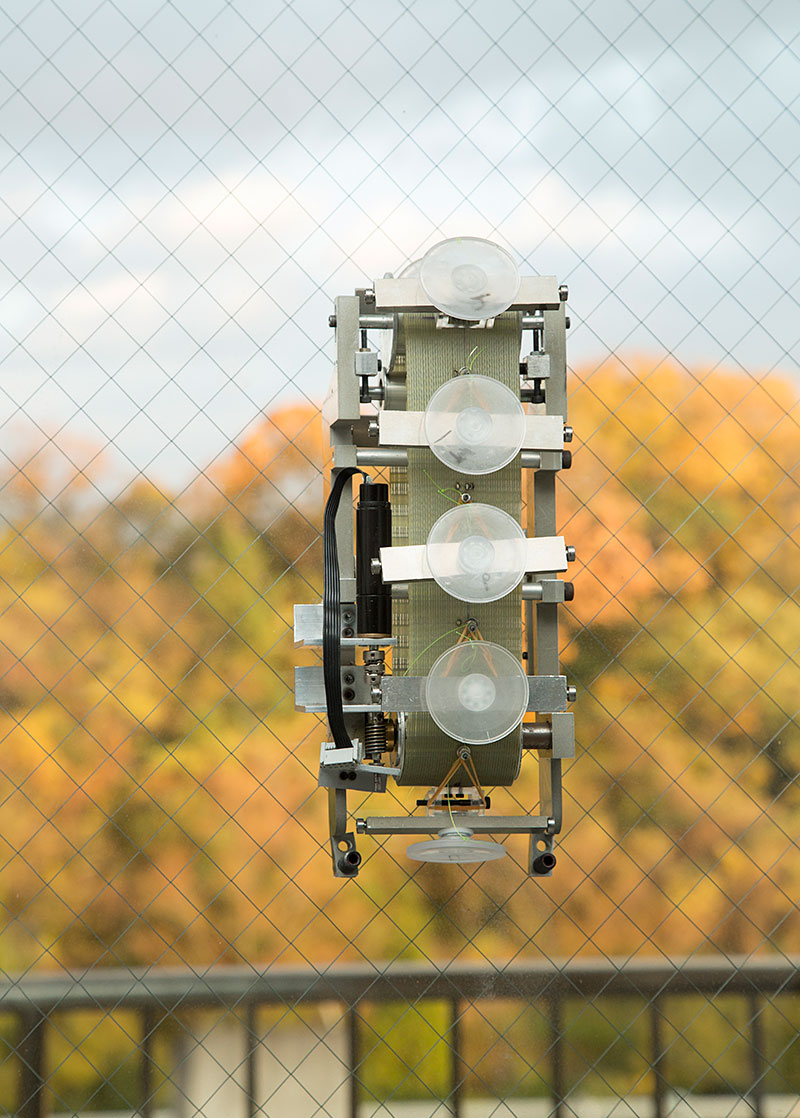
The robot is designed to climb on a vertical surface only with a well-balanced combination of caterpillars and suction cups. This robot was developed based on the design mantra that what can be done by machines should actually be done by machines.

Screw-driving, in-pipe inspection mobile robot. With the combined use of the wheels protruding from the main body to the three axis directions and the front unit capable of making a flexible movement, the robot can be moved inside a pipe while the wheels of the front unit move in a spiral path.
"For rescue operations at areas flooded by a large tsunami or typhoon, it is essential to use robots that can be operated in submerged or muddy places."
Using the lessons from their experience with the Great East Japan Earthquake of 2011, Ma and Kakogawa have been taking on a new challenge.
To make robots waterproof and dustproof, these two researchers needed to get away from conventional design ideas and make a new one from scratch. This fact also applies to the robots that they have already developed. For the most existing robots, it is impossible to maintain their original structures and functions if seals or rubber packings are additionally attached to their parts or units that must not be exposed to water or any other liquid. Ma and Kakogawa have succeeded in the development of a three-module, in-pipe inspection mobile robot that is waterproof and dustproof.
Ma said, “What we are really aiming at is to develop robots that are actually useful at disaster sites.” To this end, these two researchers are devoting themselves to research and are striving to increase the feasibility of such robots. It is highly expected that their robots will be put into practice as soon as possible.
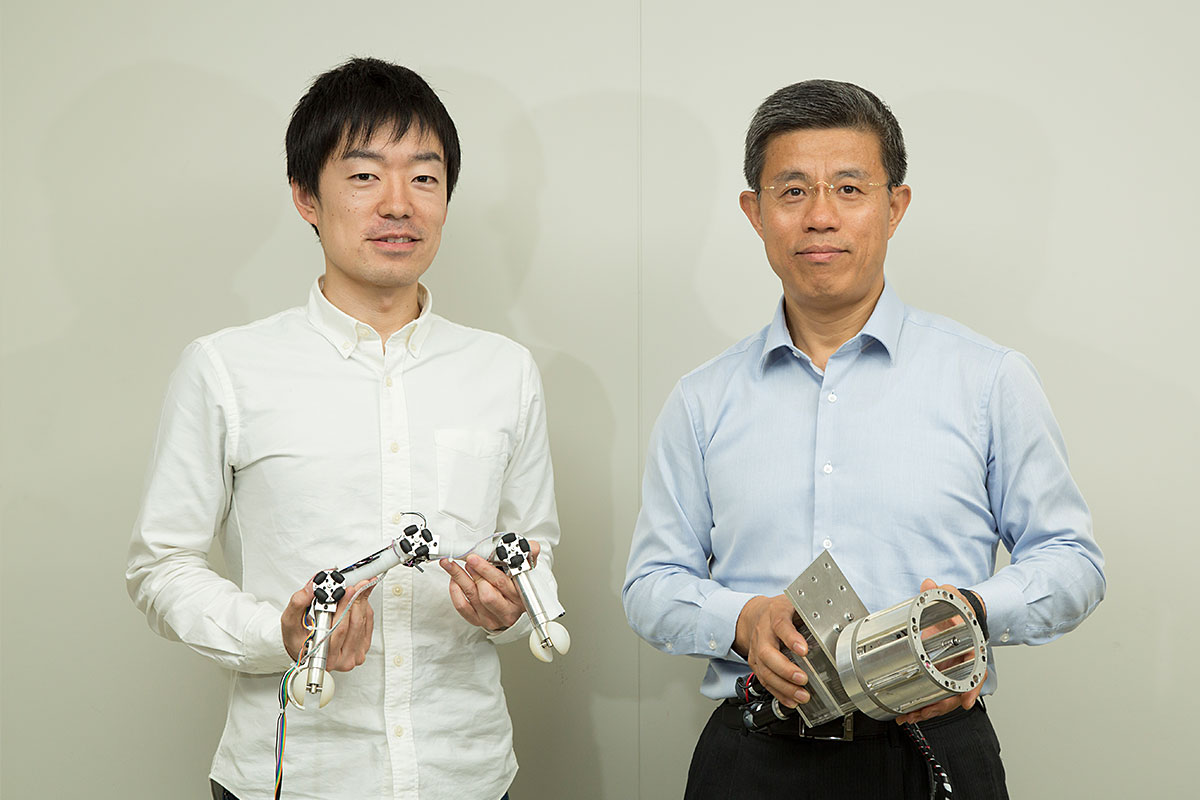
Atsushi Kakogawa [Left]
Assistant Professor, College of Science and Engineering
Subject of Research: Research and development of in-pipe inspection mobile robots
Research Keyword: Dynamics/Control, Mechanical Systems
Shugen Ma [Right]
Professor, College of Science and Engineering
Subject of Research: Research and development of the biologically-inspired robots like a snake-like robot and a legged robot, the environmentally adaptive machines like an in-pipe inspection mobile robot and a crawler robot, and rescue robots.
Research Keyword: Intelligent Robotics, Dynamics/Control, Intelligent Mechanics and Mechanical Systems