STORY #5
Robust, durable mechanical robots with a
seemingly unsophisticated appearance that are capable of fulfilling their potential at disaster sitesShugen Ma
Professor, College of Science and Engineering
Atsushi Kakogawa
Assistant Professor, College of Science and Engineering
Robots that can act as surrogates for humans to perform search and inspection operations at sites that are difficult and dangerous for humans to enter.
A long, slender snake-like robot is moving inside a long thin pipe with an internal diameter of about 75 mm. It is remarkably capable of moving up and climbing without stopping when reaching a pipe portion that bends up, down, right or left.
The robot was developed by Shugen Ma and Atsushi Kakogawa, both of whom are engaged in the development of robots capable of handling operations in places that are difficult for humans to enter, such as at disaster sites.
Reflecting upon the Great Hanshin/Awaji Earthquake of 1995, Ma said, “It was not until then that the Japanese people were strongly aware of how important robots capable of handling operations at disaster sites were.”
In residential areas where there were many wooden houses located, there were numerous buildings and houses destroyed and reduced to rubble or debris, which made rescue operations difficult. Rescue workers had trouble moving around to remove obstacles from collapsed buildings or houses and searching for people trapped in them. To prevent secondary disasters at sites hit by this kind of urban disaster, there is great demand for the development of robots that can act as surrogates for humans to handle operations at locations that are physically impossible or dangerous for people to enter.
The robot developed by Ma and Kakogawa, which looks like a snake, is designed to move in a way that is quite different from how living snakes move. Kakogawa said, “As it is difficult for a robot to creep like a snake in a long, thin pipe, we introduced snake-like structures to enable the robot to travel even in a thin, narrow location. We have also designed wheels that help the robot to move more efficiently.”
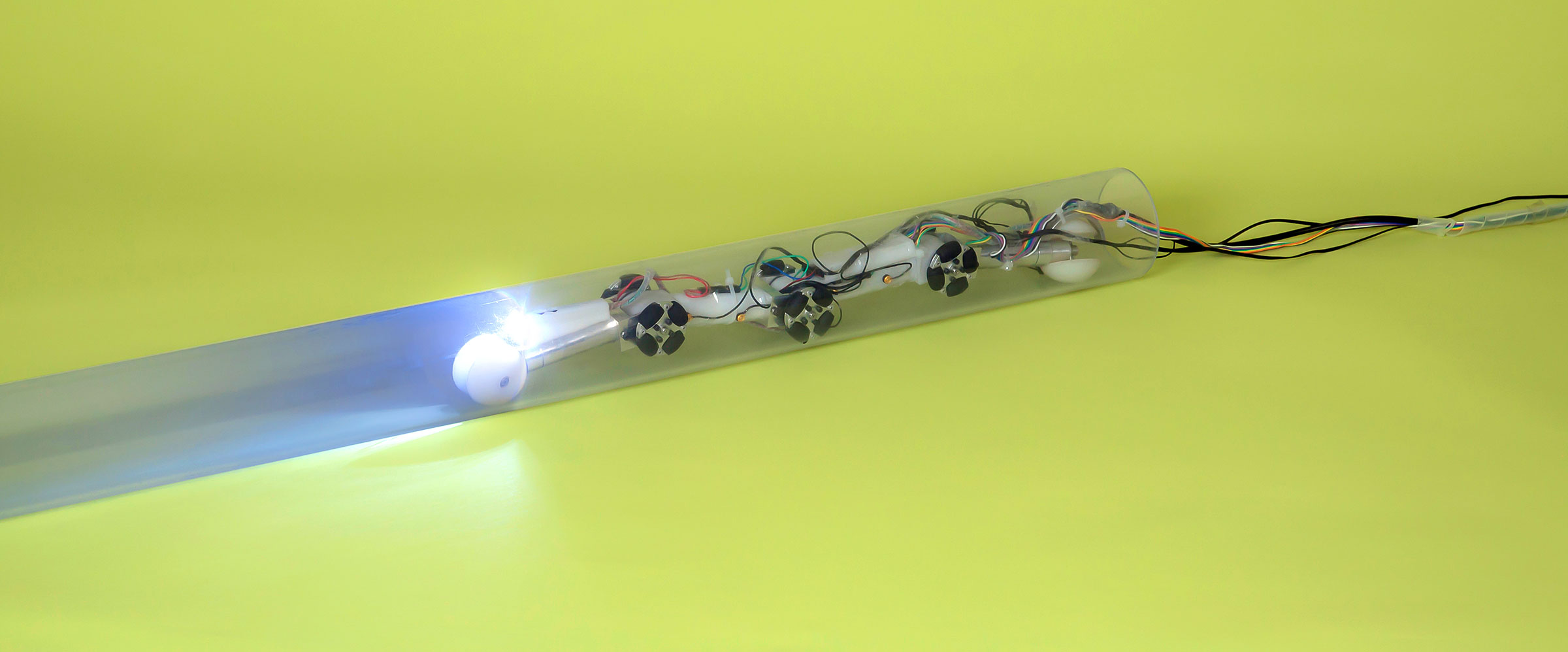
The robot consists of several body units that are connected to each other through joints with the front body unit, the rear body unit and each joint equipped with wheels. What is the most distinct about this robot is that the moving direction of the robot can be flexibly controlled towards right or left and up or down directions, even along a narrow pipe, by rotating the wheels attached to the front and rear body units. It is impossible for vehicles having wheels that are attached only to car bodies, like trailers, to move in a side to side direction because their propulsion force is applied only to forward and backward directions. The robot’s wheels attached to the front and rear units enable the side to side movement of the robot. When the robot is moved in a side to side direction inside a pipe that has a circular cross-section, the robot is capable of changing its movement direction while rolling over.
The robot is composed of several driving units that are connected to each other through joints, which allows for the generation of large propulsion even within a narrow space. Furthermore, motors, cameras, sensors and other devices can be installed on the robot if more joint parts are added to the robot as needed. As the number of motors required to drive the robot is less than those of traditional robots, the maintenance of the robot is much easier. To enable the robot to support both autonomous movement and remote control operations, Ma and Kakogawa are working to make improvements with the goal of putting it into practical use within five years.
When it comes to the application possibilities for this robot, Kakogawa said, “The robot is expected to be used to make regular inspections of the inner conditions of pipes to check for deteriorated parts or flaws before a natural disaster occurs, in order to prevent a large accident.”
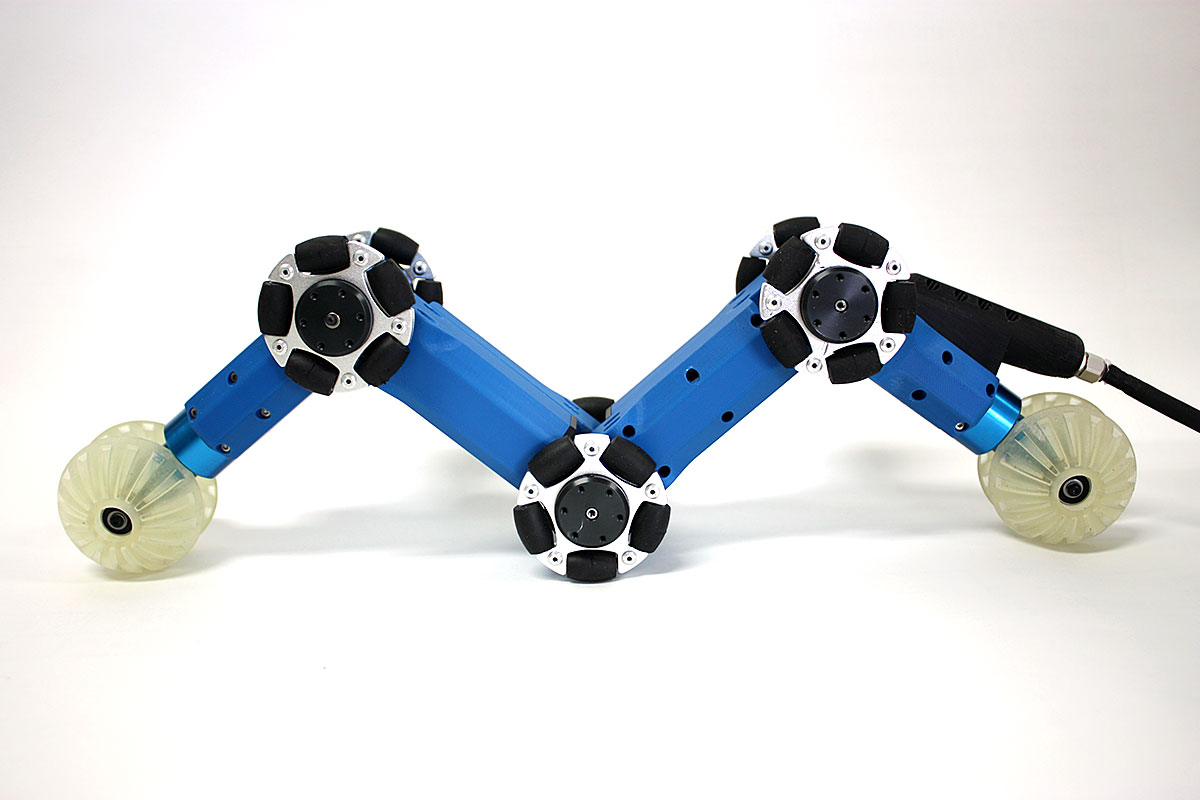